Why you need APQP
Developing new products and improving production processes are essential if you want to establish or maintain a competitive advantage in global markets. However, process innovation and product development must be managed to minimise the risks of technical and commercial failure.
Advanced Product Quality Planning (APQP) enables you to identify, control and eliminate the risk of failure, by ensuring that:-
- The customer expectations and market requirements areunderstood, defined and quantified
- Development projects are commercially viable – with a sound bussness case
- Designs satisfy the market requirements
- Production processes are capable of producing the chosen design
- Supply chain partners are also reliable partners
Using APQP, companies are able to create a product development process that:-
- Is faster and more responsive to changing market requirements
- Delivers better quality products and services at lower cost
This is achieved by creating an ‘ideas factory’ that allows information and data to be created, processed and validated as it flows through the development process. Each process step has clearly defined inputs and outputs with established communication links to adjoining processes and sub-processes.
As technology develops new tools and techniques become available to help improve our decision making, for example, computer simulations and rapid prototyping are now used routinely. To remain competitive, we need to exploit the benefits that each technical advance brings, and select the most appropriate tools for each product and project. However, the ability to manage the information flow and validate the choices that are made remains a critical success factor.
When responsibility for development is shared between supply chain partners – or internal teams in different locations – collaboration may become more important, but difficult without a common approach to communication and status reporting.
The APQP Standard developed by the Automotive Industry Action Group (AIAG), first published in 1994 and revised in 2008, addresses the need for a:-
- Common development processes
- Common tools and techniques to identify and eliiminate problems
- Standardised terminology use to communicate with supply chain partners
- Standardised offormats for reporting project information
Ensuring that decisions are well informed and evidence based is critical to the success of the project and barriers to communication must be broken down.
APQP - The Automotive Standard
Working with the Automotive Industry Action Group (AIAG), vehicle manufacturers agreed to:-
“Standardise their reference manuals, procedures, reporting formats, and technical terminology – to be used by suppliers implementing APQP Techniques”
The resulting standard was first published as part of the QS-9000 quality initiative, is now maintained by AIAG, and within the TS16949 quality standardis recognised as a possible customer requirement for component suppliers.
The standard identifies the essential elements or stages of a development program, and describes the development activities using an input – output model.
The automotive standard also provides:-
- Templates or standard forms that can be used to document the outputs from particular process steps
- More detailed guidance in separate publications. explaining how to use some of the recommended tools and techniques. Known as the core tools include the use of Failure Modes Effect Analysis (FMEA),Statistical Process Control (SPC), Measurement System Analysis(MSA) and a recommended Production Part Approval Process (PPAP)
The level of risk associated with particular failure modes is determined by considering:-
- The effects the failure will have when it occurs (Severity), and
- The chance that the causes of failure will be present (Occurrence), and
- The ability to detect when the error condition is present (Detection) allowing the effects of failure to be prevented or minimized.
Reading this page on your computer, relies on the ability of equipment supplied by different companies to create, transmit, receive and interpret data using a communication protocol. Integrating IT equipment fromdifferent suppliers using this ‘plug and play’ technology is now taken for granted. Adopting common standards is the key to collaboration – and theAPQP standards enable supply chain partners to become a development team, with management systems that can plug and play together and reducing the risks of collaboration.
Adopting APQP and the documentation(standard forms) provided by AIAGenables suppliers to communicate with potential clients more effectively and ensures that supply chain partners have a common understanding of the project status and requirements.
The standard sets creates common requirements where different manufacturers have been able to align and standardise their systems, while each company may retain its own customer specific requirements. These may explain how they interpret the standard, or give more detailed guidance on particular topics.
Suppliers therefore need to develop a good working relationship with their clients and ensure that they understand their customer specific requirements
However, the standard is based on the information content – not the technology used so it does not prescribe the use of particular ‘off the shelf solutions’ . This allows organisations to select the ‘best available technology’ for their product or process, while collaborating with their clients and suppliers.
Mapping the Development Process
APQP recognising and encourages the systematic use of formal and tools techniques to improve decision making throughout the development process. Good communication and standard forms may improve information flow and provide an audit trail but APQP is more than a collection of formsproduced to satisfy the auditors.
APQP creates a development process with logical links between processes and sub-process that can be mapped as shown on the right:-
Describing and mapping the development process as a set of inter-dependent sub-processes with expected inputs and outputs highlights the purpose of each process, and creates a common understanding of the process and value chain.
Managers implementing APQP must understand the purpose and value of each activity and be committed to:-
- A process based approach to product development
- Evidence based decision making
- Professional and personal integrity
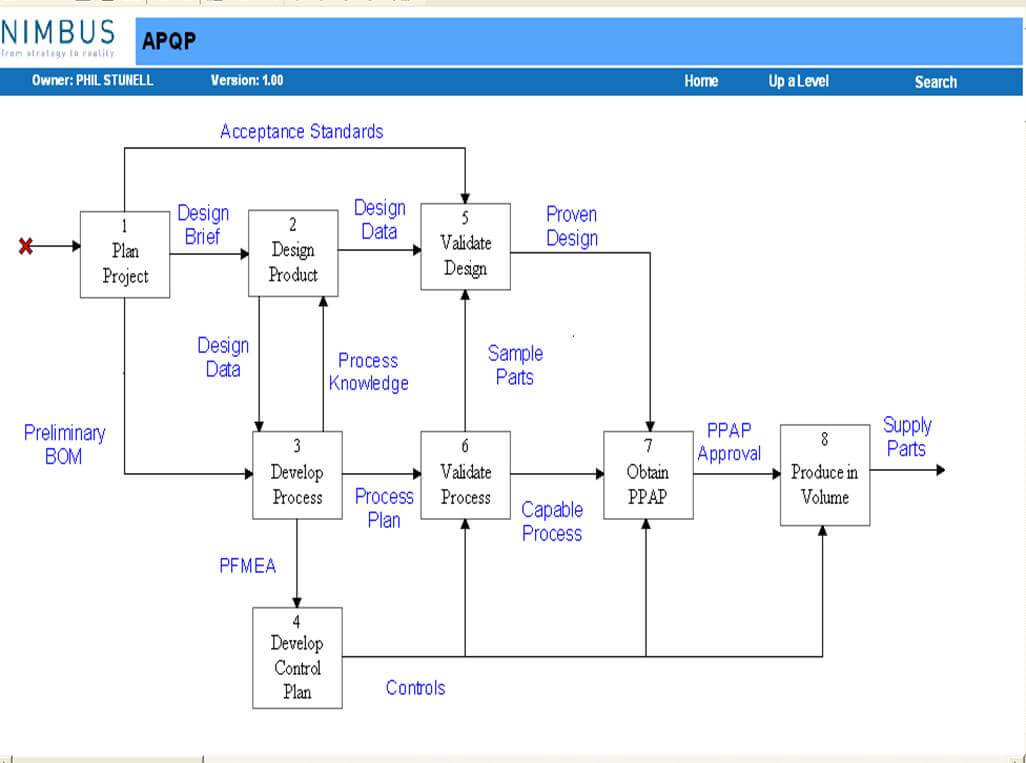
Good documentation of the input and outputs from development activitiesprovides an audit trial and traceability – so we know when important decisions were made – and assumptions made.
The APQP process provides evidence to guide and improve decision making, so supplying miss-leading information by design or accident may have serious technical and commercial consequences anddestroys trust
The AIAG standard forms and templates are useful aids to communication, and when used correctly provide evidence that the APQP process has been applied.
APQP Training and Support
Phil Stunell is an experienced engineer with practical experience of product development, using APQP and the core tools to deliver successful products. He understands that APQP is about the systems and processes used to develop new products and process – and that the standard forms and templates are an aid to communication and not the ultimate goal of the process.